When Srirangan returns home, he first picks off the hardened latex that has dried on his hands. The 55-year-old has been tapping rubber trees since he was a teenager and is familiar with the milky latex that turns hard and brown as it dries. Getting it off his hands once home is an important chore.
His day begins at six a.m. when he walks across to his rubber plantation in Surulacode village armed with a hook-shaped paal veetura kathi (rubber tapping knife), six-seven inches long. The five-acre farmland, allotted to his father by the government, is a five minute walk from his home and he grows rubber, pepper and cloves on it.
Both he and his wife, Leela Srirangan who he married 27 years ago, work on the rubber trees. They belong to the Kanikaran Adivasi community.
Srirangan (who only uses his first name) starts by collecting the dry latex that has drained into a black cup he had tied to the tree the earlier day. “This is ottukara ,” he says, explaining that, “it is the leftover latex that flows into the cup after we collect that day’s fresh latex. It dries overnight.”
Selling dried latex is an added income which gets them anywhere between Rs. 60-80 per kilo. They sell the ottukara in the market after collecting it for two weeks.
Once he has emptied the cups, he cuts an inch-long strip into the bark of the tree for fresh latex to flow into the cup. He repeats this process for the remaining 299 trees on his land.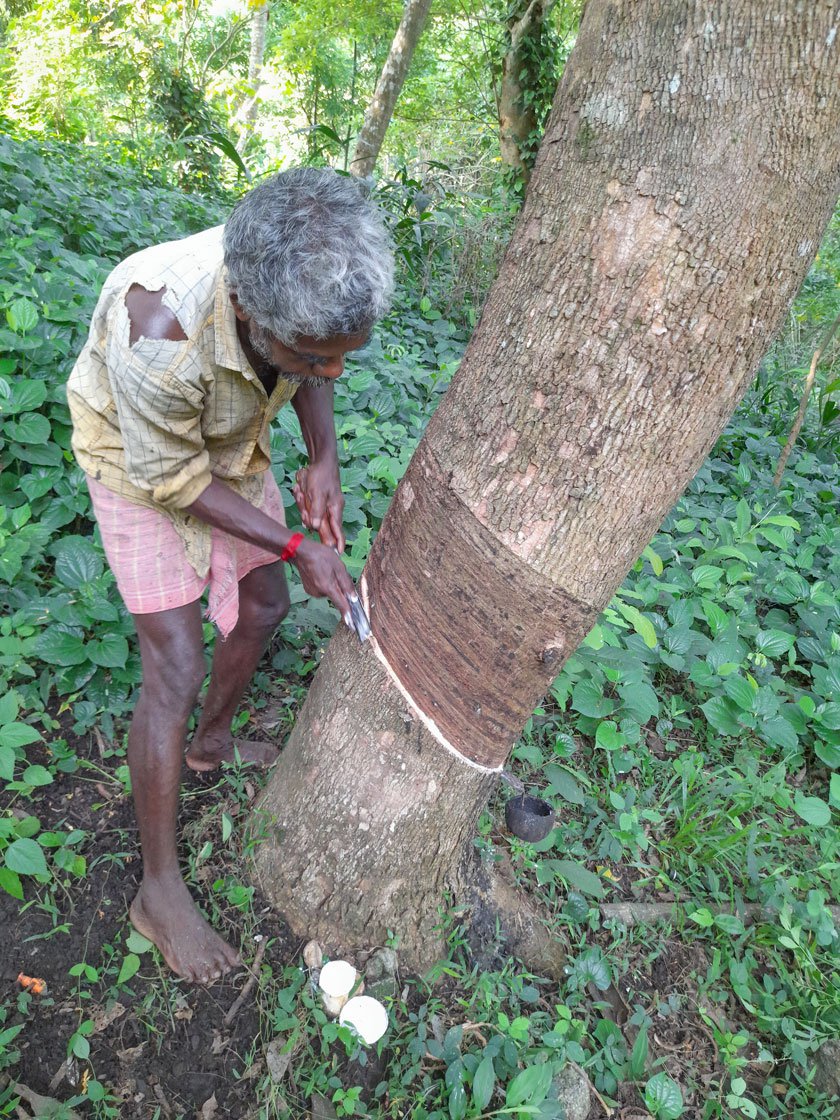
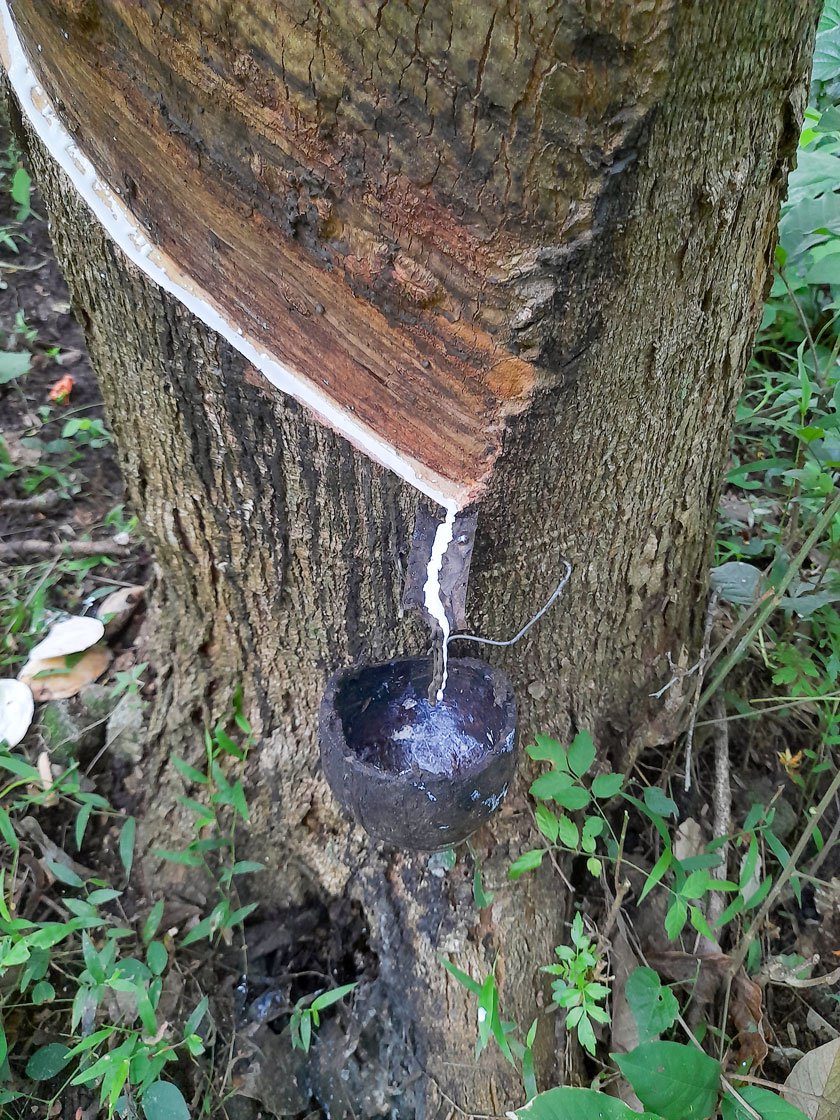
Srirangan tapping rubber trees in his plantation in Surulacode village. He cuts a strip from the bark; latex flows into the black cup
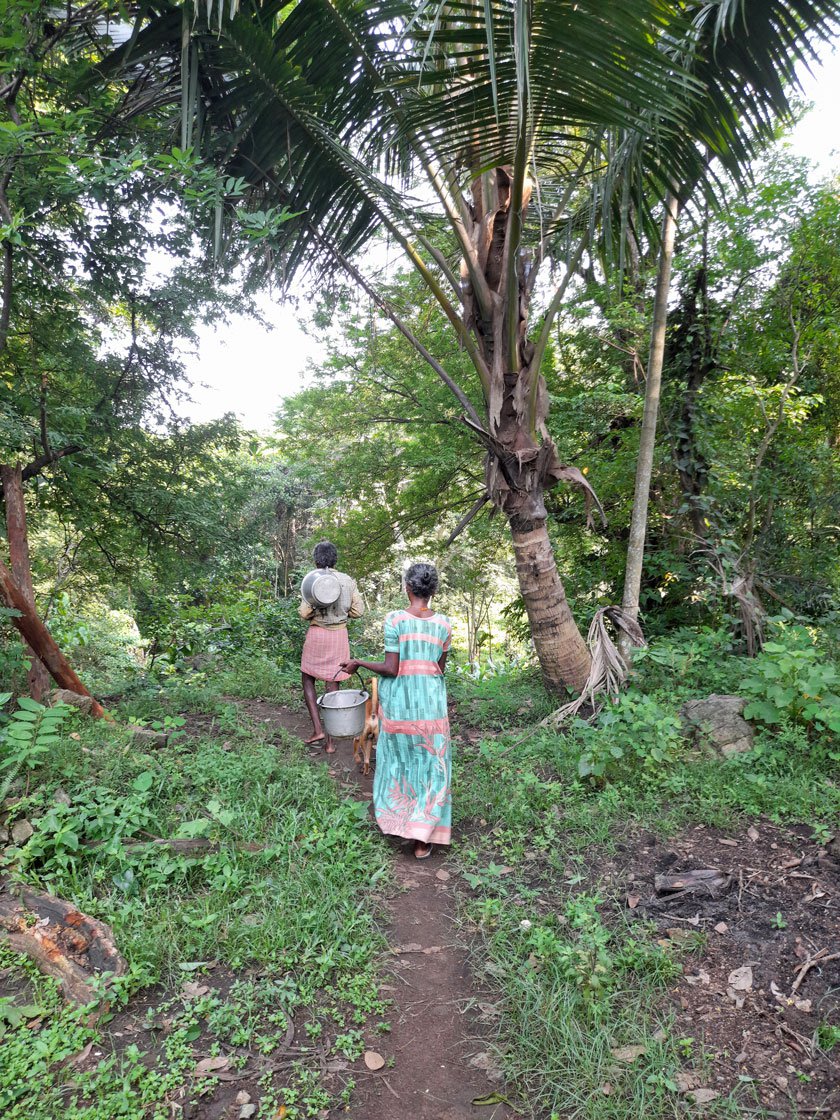
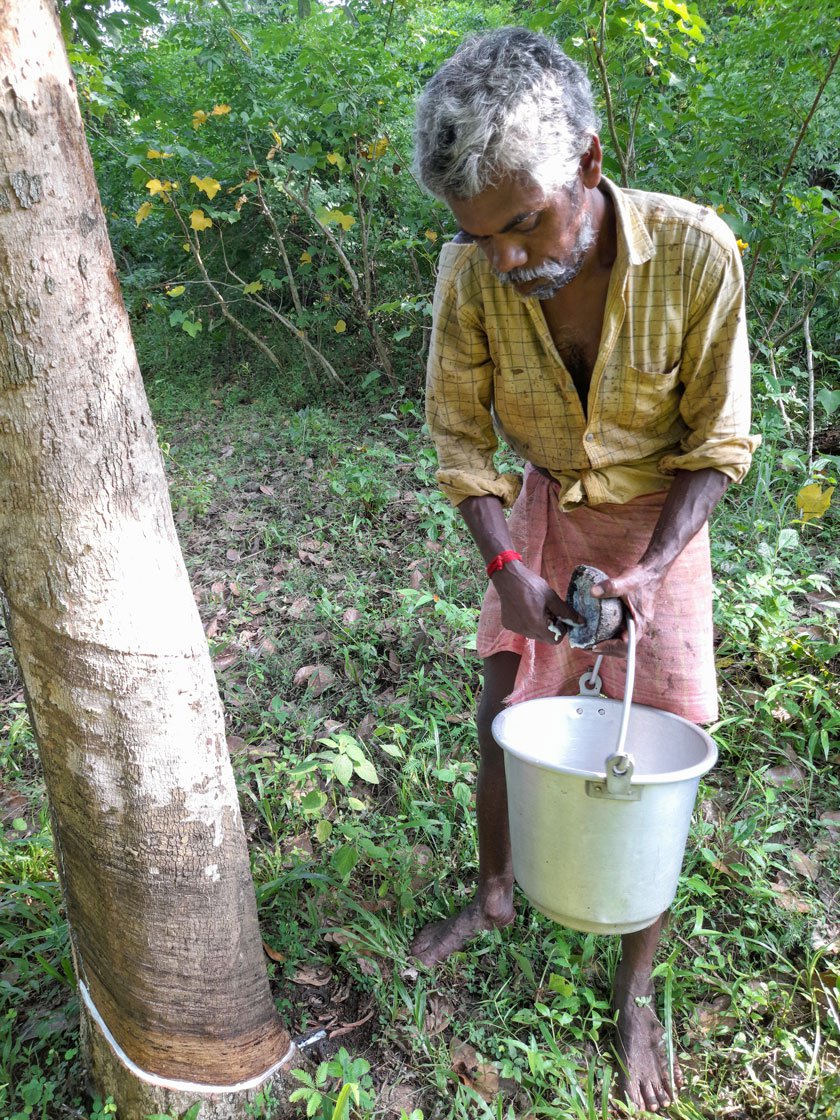
After breakfast, Srirangan and Leela walk back with buckets (left) in which they collect the latex in (right)
When Srirangam is out working his rubber trees, Leela finishes house work and makes breakfast. After three hours of rubber tapping, Srirangan comes home to eat. The couple live near the Thottamalai mountain; the Kodaiyar river runs close by. They live alone – their two daughters are married and live with their husbands.
Around 10 a.m., Leela and Srirangan return to the plantation, carrying a bucket each to collect the milky-white latex that has drained into the cups. The process takes them an hour and a half and they get home by noon. There is no time to rest, the process of making rubber sheets must begin immediately or the latex starts drying.
Leela begins mixing the latex with water. “If the latex is thick, we can pour more water. But it will take a lot of time to turn it into sheets,” the 50-year-old says.
Leela sets the rectangular vessels as Srirangan pours the mixture into them. “We fill this vessel with two litres of latex and a small amount of acid. The amount of acid depends on the amount of water used. We do not measure it,” says Leela, as her husband finishes pouring the latex into the moulds.
When PARI visited them in May, the rubber season was just beginning and they were getting only six sheets in a day. As the season goes on till March, they can make upto 1,300 sheets for the year.
“A single sheet contains 800-900 grams of latex,” explains Srirangan. Leela carefully starts mixing the acid in.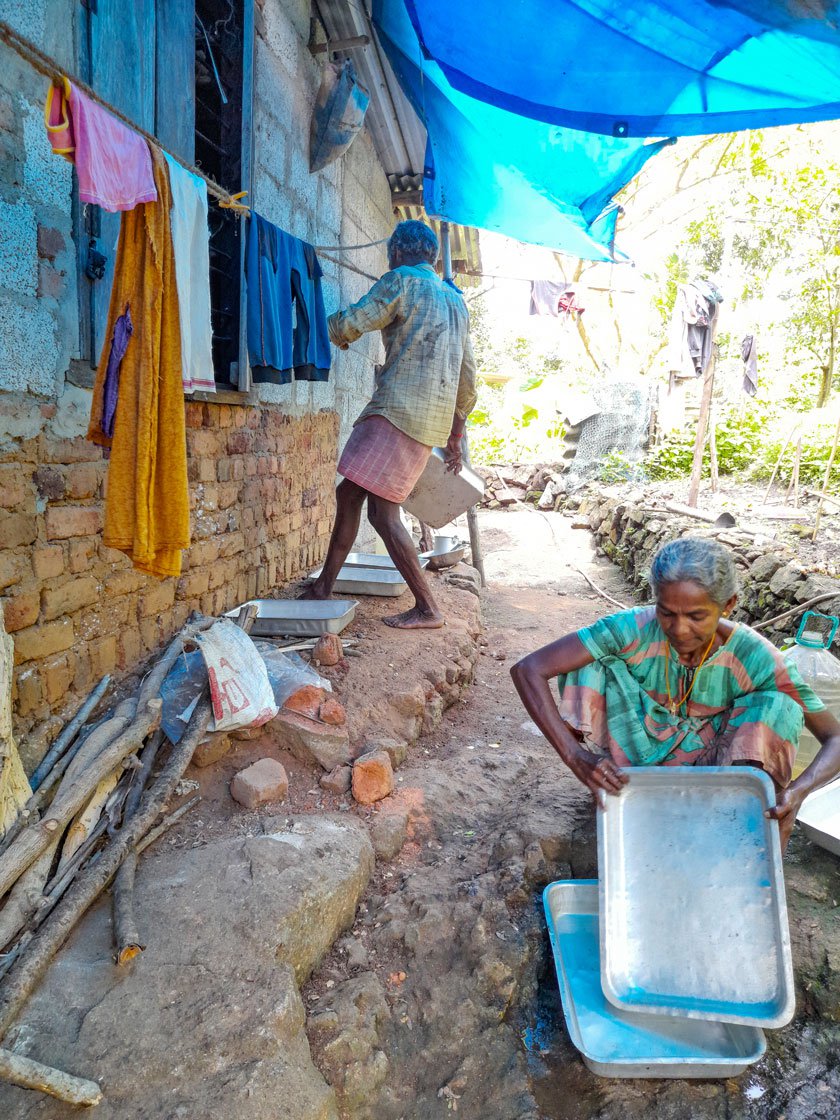
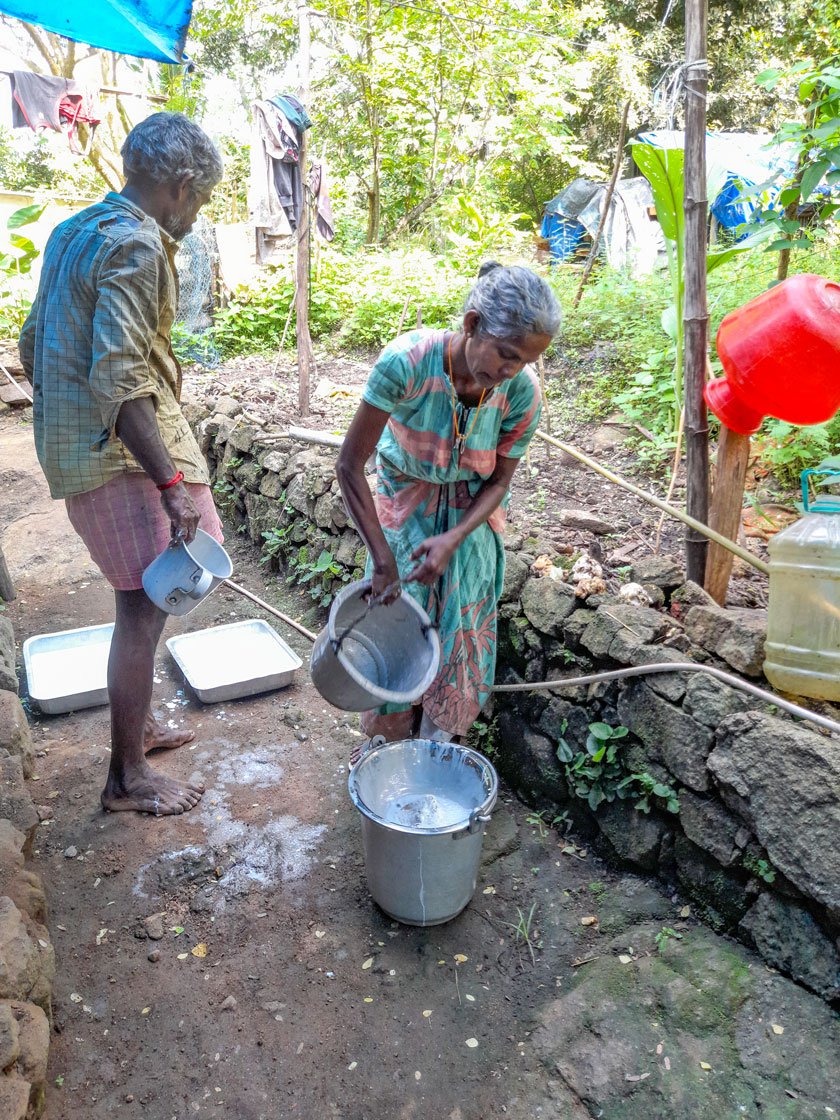
The couple clean and arrange (left) rectangular vessels, and then (right) mix the latex with water before pouring it in
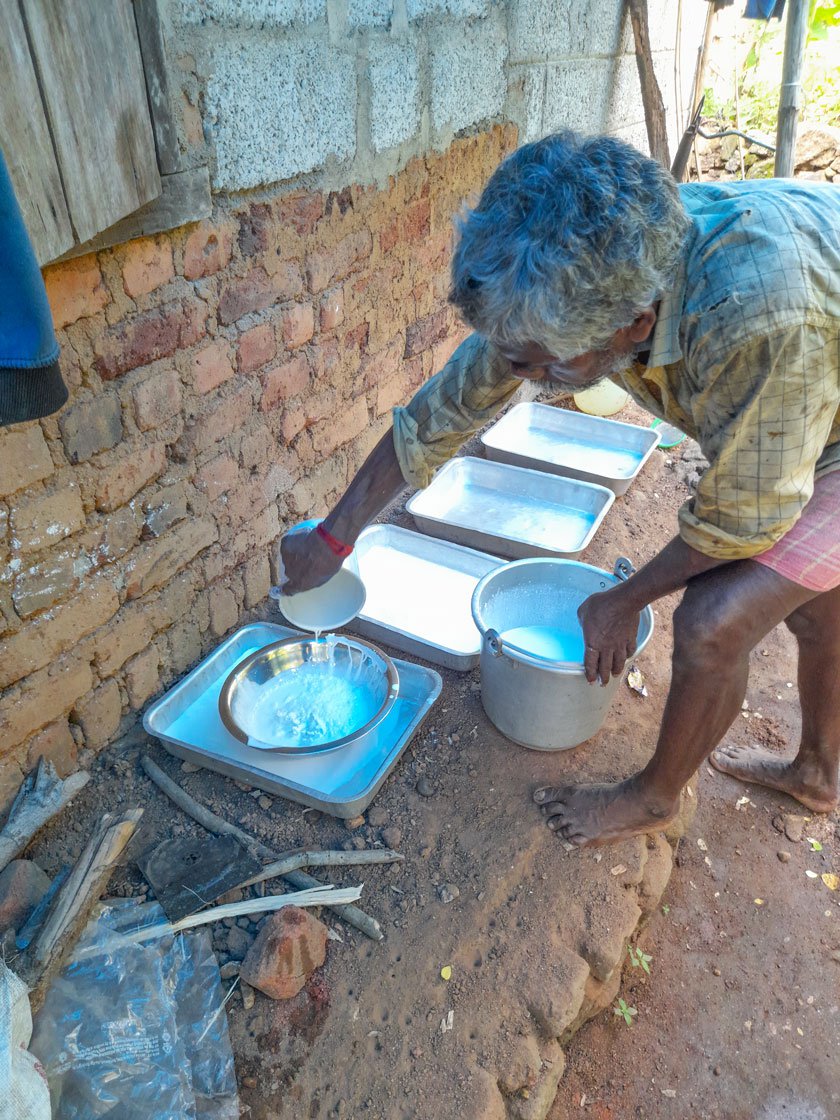
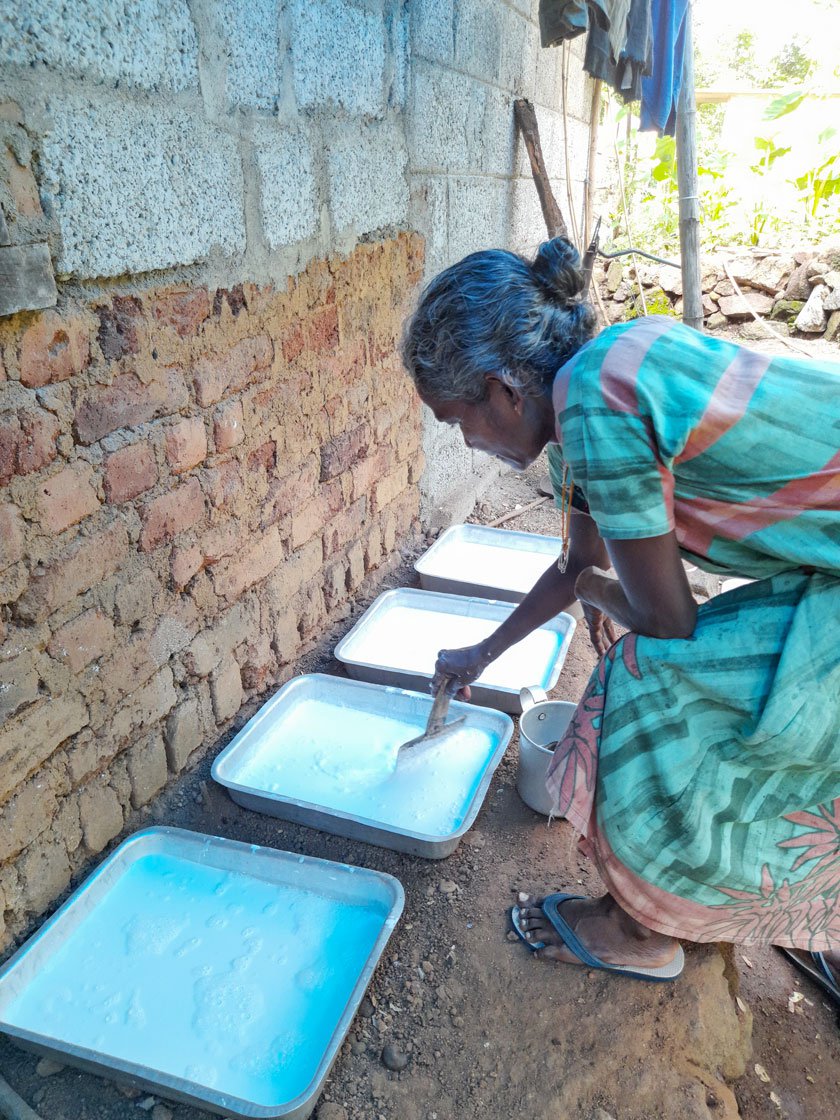
Srirangan pours the latex into the vessel using a filter (left); Leela mixes some acid in it (right) so that it coagulates
After 15 minutes, the latex coagulates and the process of turning it into rubber sheets begins. The latex is inserted into two types of roller machines. The first machine is used four times to thin out a single sheet evenly, while the second one is used once to give it shape. The sheets are then cleaned with water. “Some usually hire a labourer and pay two rupees per sheet [they make]. But we prepare these rubber sheets on our own,” says Leela.
The moulded rubber sheets are first dried out in the sun. Srirangan and Leela hang the rubber sheets on a line, which they sometimes use to hang their clothes. The next day, they take the sheets to their kitchen.
Leela removes a small curtain to reveal a bundle of rubber sheets hanging above the firewood. “The heat from the fire dries the sheets. When the sheet becomes brownish, you will know it is completely dried out,” she explains, taking out a rubber sheet from the bundle.
The couple collect the sheets and sell them to a rubber sheet shop eight kilometres away when they require money. “There is no fixed price,” says Srirangan. The income they get changes daily according to the market rate. “For now it is 130 rupees per kilogram,” he adds.
“We have got around 60,000 [rupees from rubber sheets] in the last year,” he says. “We cannot go for rubber tapping if it is raining or too hot,” says Leela. On those days they just have to wait it out.
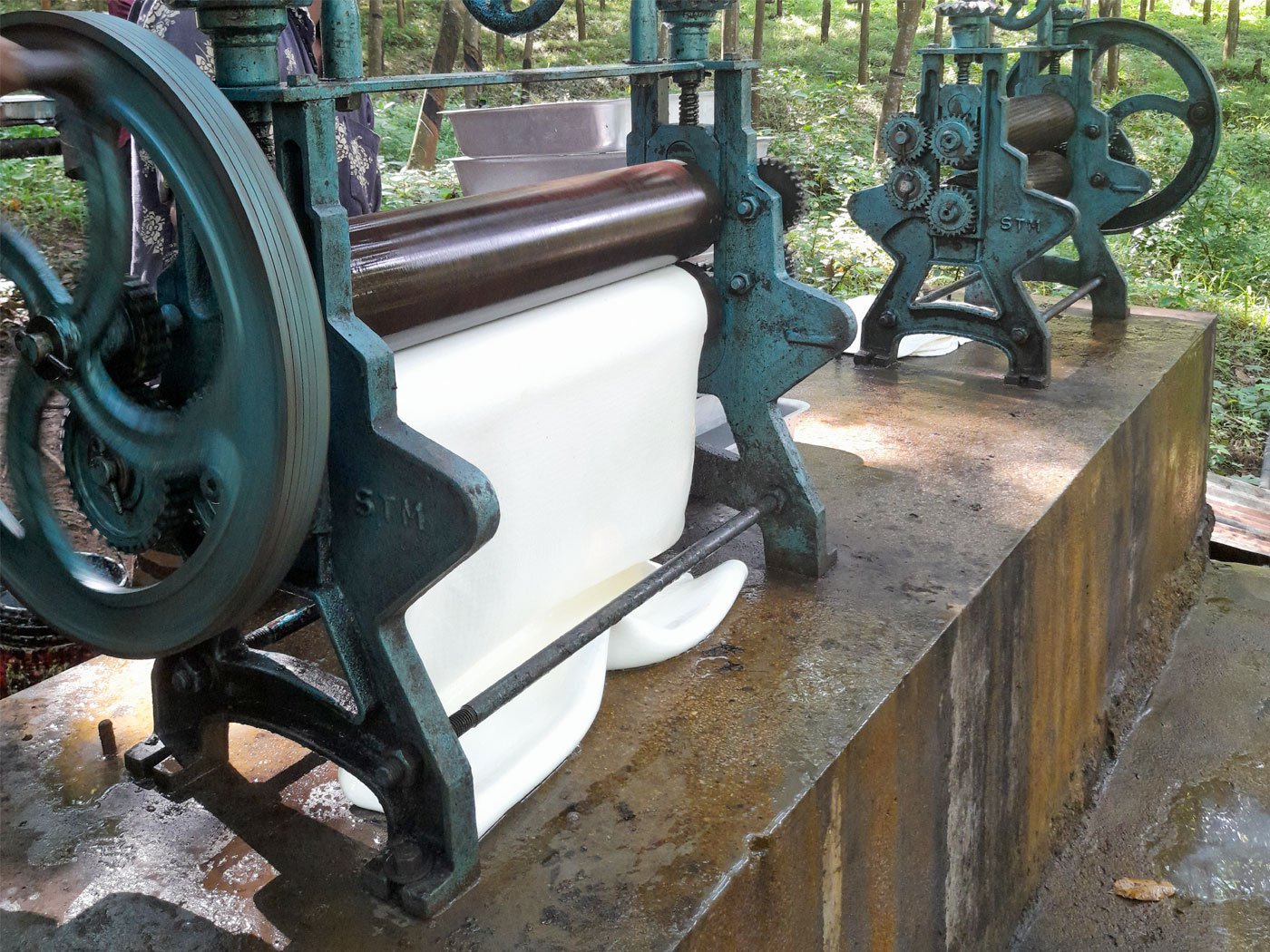
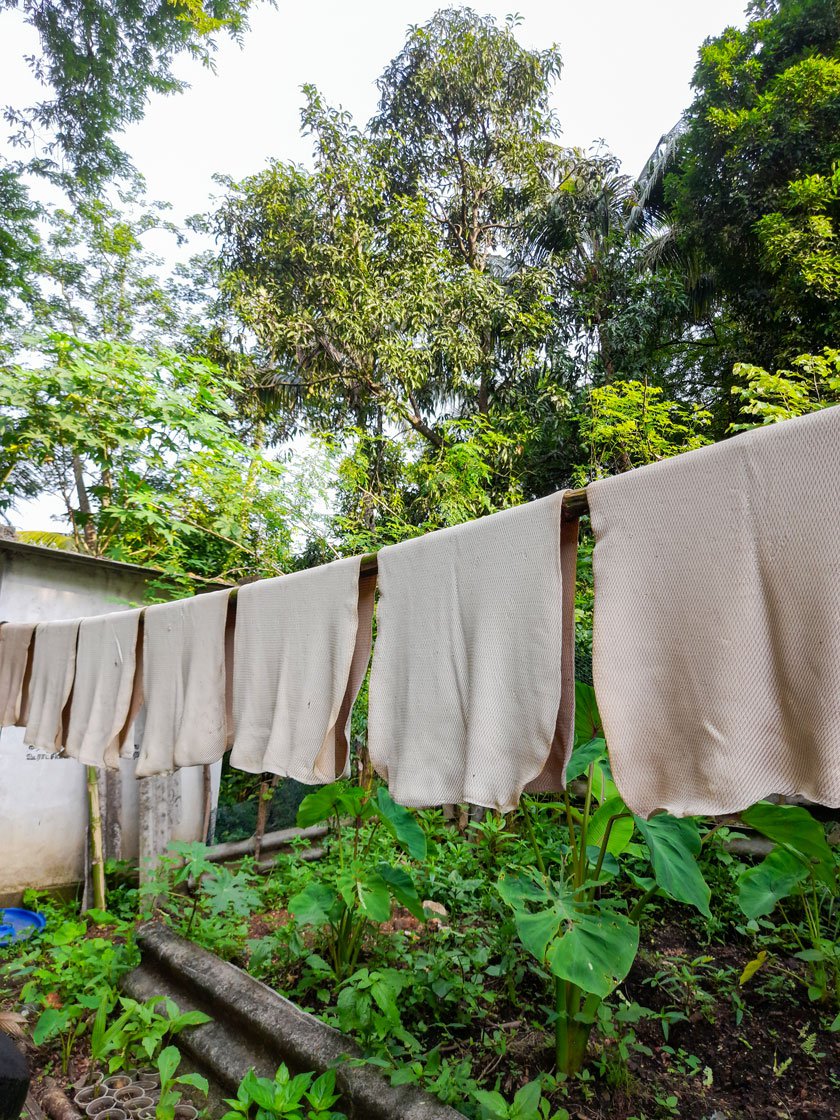
Left: The machines in which the coagulated latex thins out and gets a shape. Right: The sheets drying in the sun
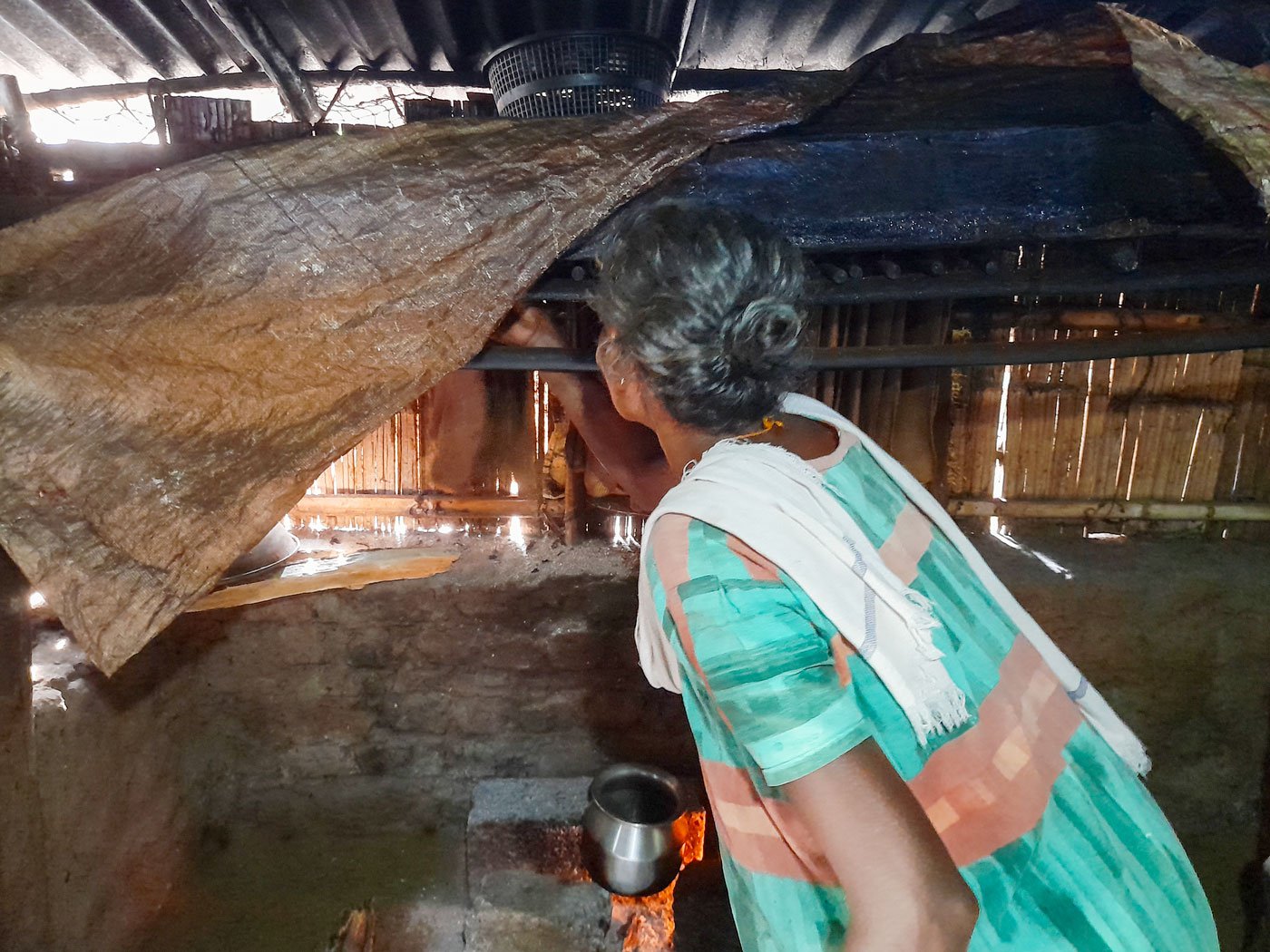
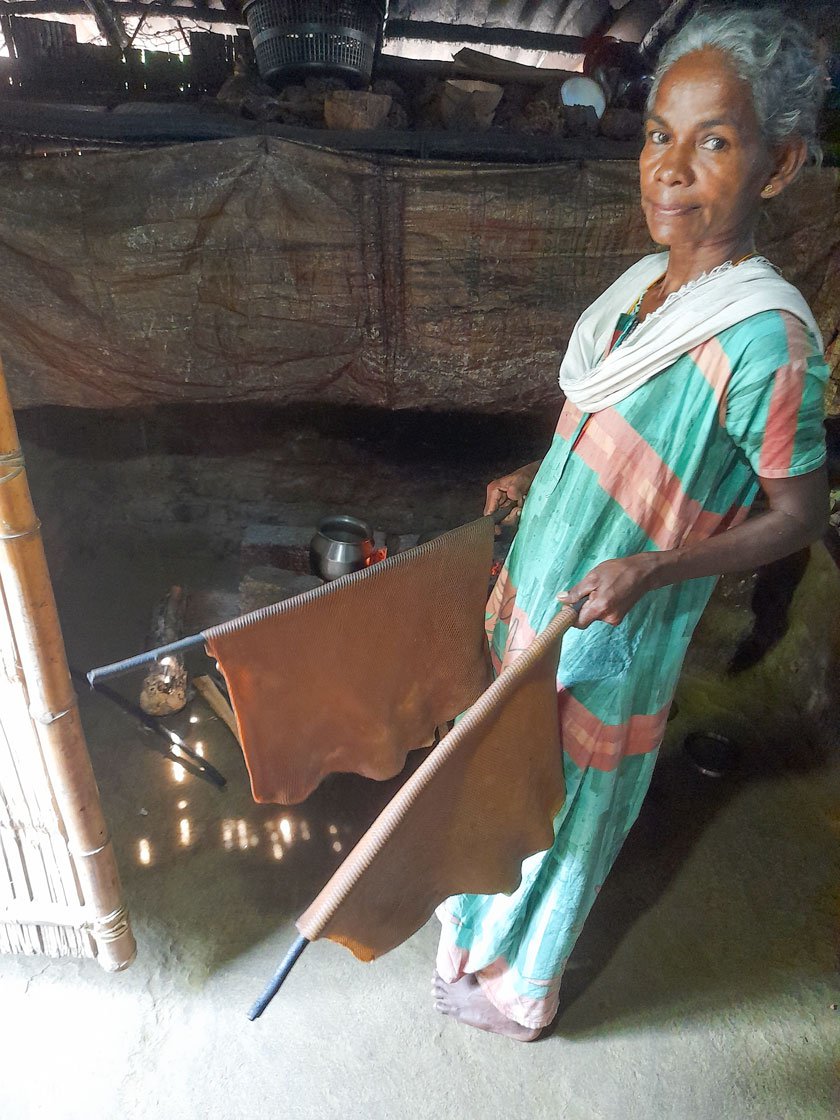
To dry them out further, the sheets are hung in the kitchen. 'The heat from the fire dries the sheets.' says Leela. They turn brown in colour when dry
The rubber trees are usually cut down after 20 years as the amount of latex they produce reduces over time. New saplings are planted in its place and it takes seven years for the newly planted rubber tree to produce the required latex. “Sometimes people also cut the trees after 30 or 15 years. It depends on the amount of latex the tree can produce,” says Srirangan.
According to data by the Government of India’s rubber board , the area under rubber cultivation has increased by around 38 per cent in the last fifteen years, and the yield has decreased by 18 per cent in the same time.
“The profit for our work also changes according to the season,” says Srirangan. So they also have other sources of income – they harvest pepper and cloves once a year.
“For the pepper season, the profit will be based on the amount of pepper sold in the market. It is similar to all other crops like cotton. Around this time [May], we get 120 [rupees] for one kilo of green pepper. For one clove, we get 1.50 rupees,” he adds. In a good season, they can manage to collect up to 2,000- 2,500 cloves.
Srirangan has also been the oor thalaivar (hamlet head) since the last 15 years. “The people chose me because of my good oratory skills. But I cannot look after everything anymore because of my old age,” he says.
“I managed to bring a primary school [GPS-Thottalamalai] to the village and encouraged the construction of the road,” he adds happily.