It takes Fahmeeda Bano a month to spin enough thread for a regular-sized pashmina shawl. Separating and spinning the fine, gossamer-like wool of the Changthangi goat is an arduous and delicate task. The 50-year-old artisan says she can expect to earn roughly Rs. 1,000 for her month-long labour. “If I work continuously, I can earn 60 rupees a day,” she adds, breaking it down.
That’s a negligible fraction of the price the highly valued shawl will sell for – anything from Rs. 8,000 to over Rs. 100,000 depending on the needlework embroidery and the intricacy of the woven patterns.
Traditionally, hand spinning of pashmina thread was done by women in between household work. The low wages for spinners like Fahmeeda have led to a sharp fall in the number of artisans willing to do this work.
Firdousa is another resident of Srinagar who used to spin wool before she was married and got busy taking care of her family and home. Recalling her younger days she says, “Elders in the family would urge us to spin, saying it would keep our minds occupied, rather than indulging in gossip.” Her two teenage daughters don’t spin, as they don’t find the time between their academics and household work. And then the money isn’t much.
Spinning is a part of Kashmiri culture, says Firdousa, and refers to the link between the local delicacy, nadru (lotus stem) and spinning: “Earlier women would compete with each other to spin a thread which was as fine as the fibre in a lotus stem."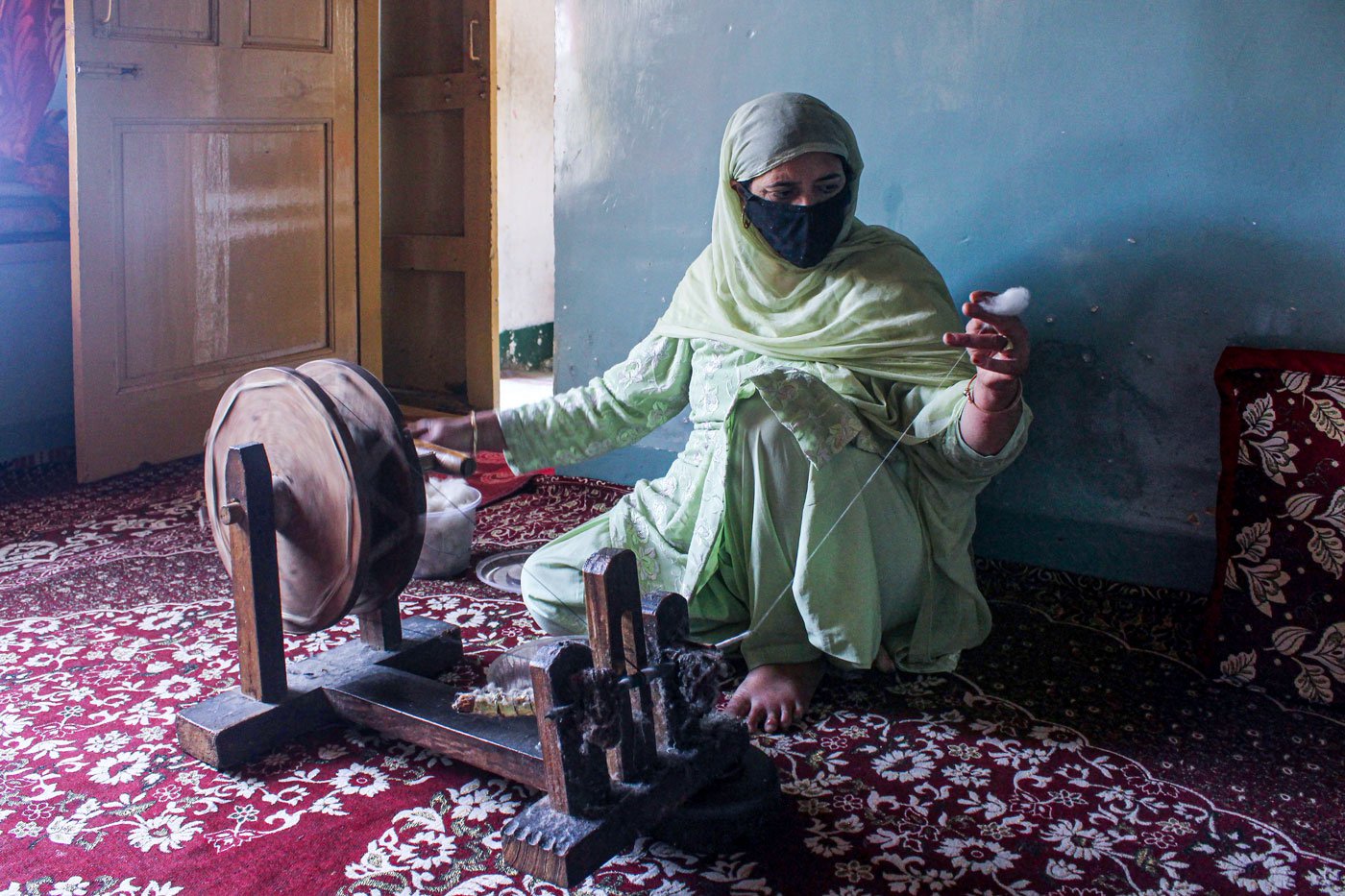
Fahmeeda Bano usually takes a month to spin enough thread for a regular-sized pashmina shawl
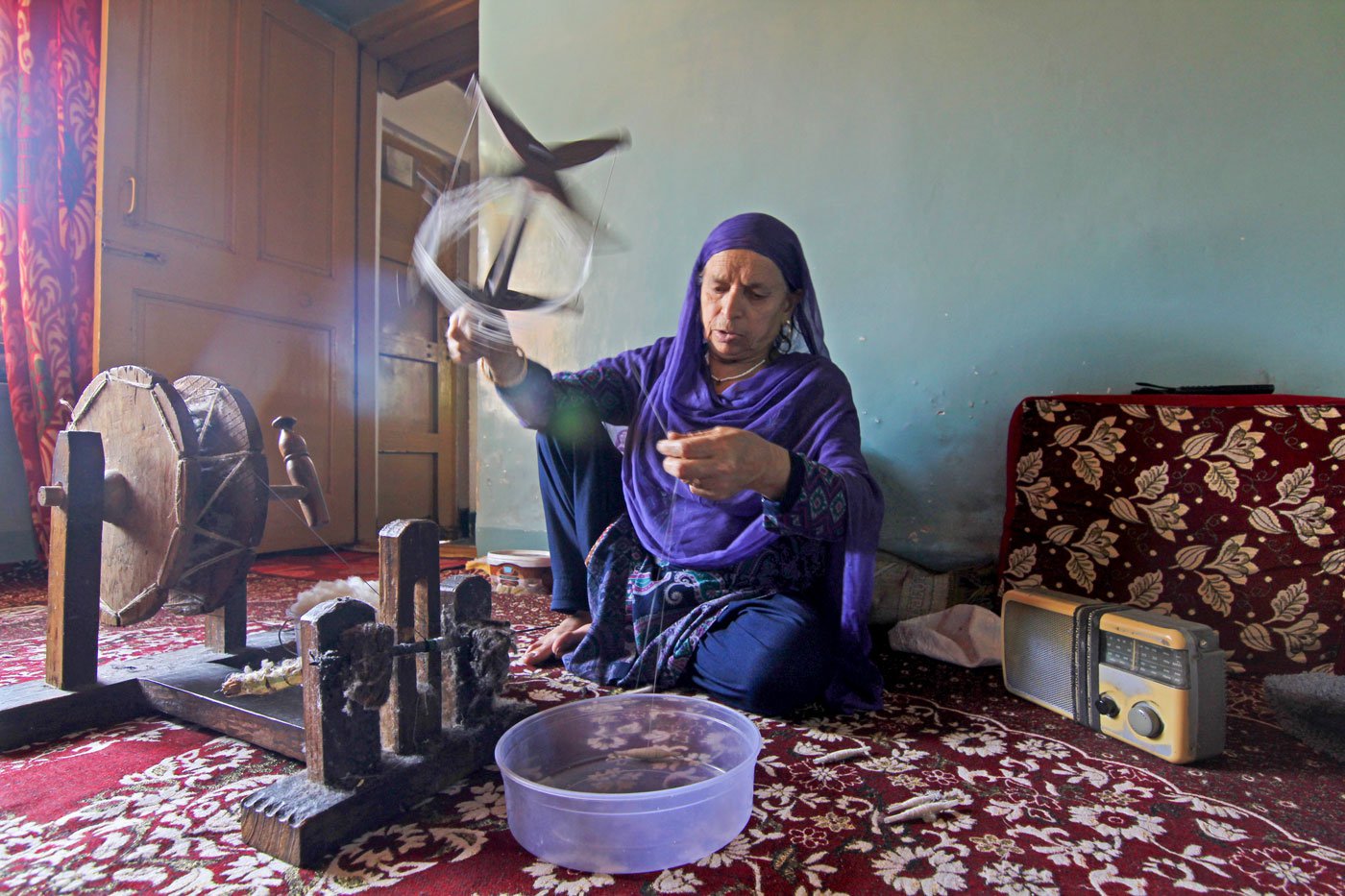
Fahmeeda's mother-in-law, Khatija combines two threads together to make it more durable
Unlike spinning, weaving of pashmina pays better and is
done by men who may switch between other jobs which pay more. Today in the union territory of Jammu and
Kashmir, an unskilled worker can expect a daily wage
of Rs. 311, a semi-skilled worker Rs. 400 and a skilled worker Rs. 480 a day,
says a 2022 J&K state notification
on wages.
A regular-sized shawl has 140 grams of pashmina wool. It usually takes Fahmeeda two days to complete spinning 10 grams of raw pashmina wool of the Changthangi goat ( Capra hirecus ) that lives at high altitudes.
Fahmeeda learnt the art of hand spinning pashmina from her mother-in-law, Khatija. The women live with their families in a single storey house in Koh-i-Maran in Srinagar, capital of the union territory of Jammu and Kashmir.
Khatija is working on her yinder (spinning wheel) in a 10 x10 feet room in her house. One room is used as a kitchen while another has a pashmina weaving workshop where male members of the family work; the rest are bedrooms.
The 70-year-old veteran spinner bought 10 grams of pashmina wool a few days ago but has still not processed the lot into fine thread as she struggles with poor eyesight. She had her cataract removed 10 years ago and finds it difficult to concentrate on the delicate spinning.
Spinners like Fahmeeda and Khatija first clean pashmina wool by ‘carding’ – pulling it through a wooden comb to make sure all the wool fibres are untangled and aligned in one direction. Then they spin it on a spindle made of twisted dried stems of grass.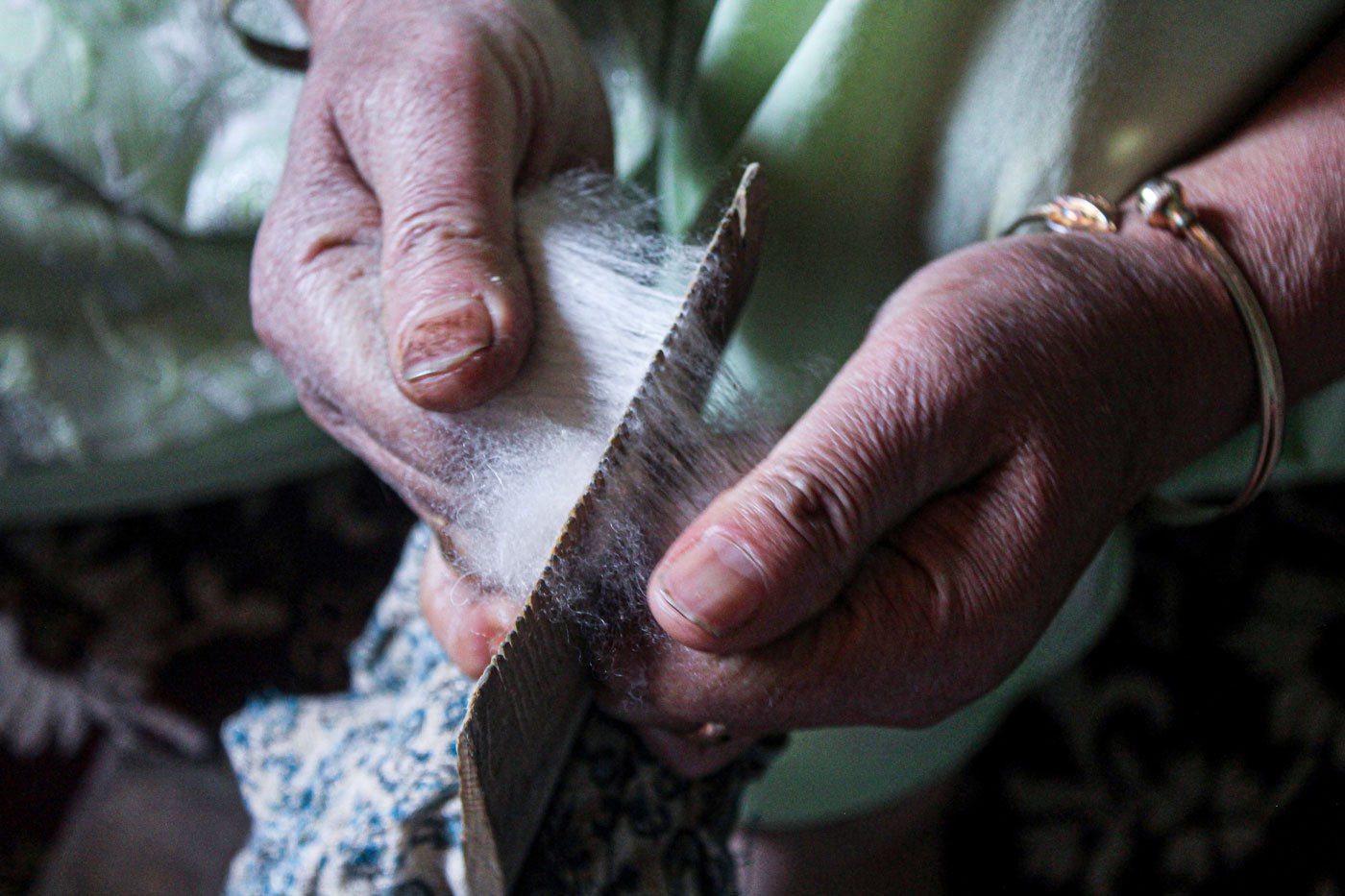
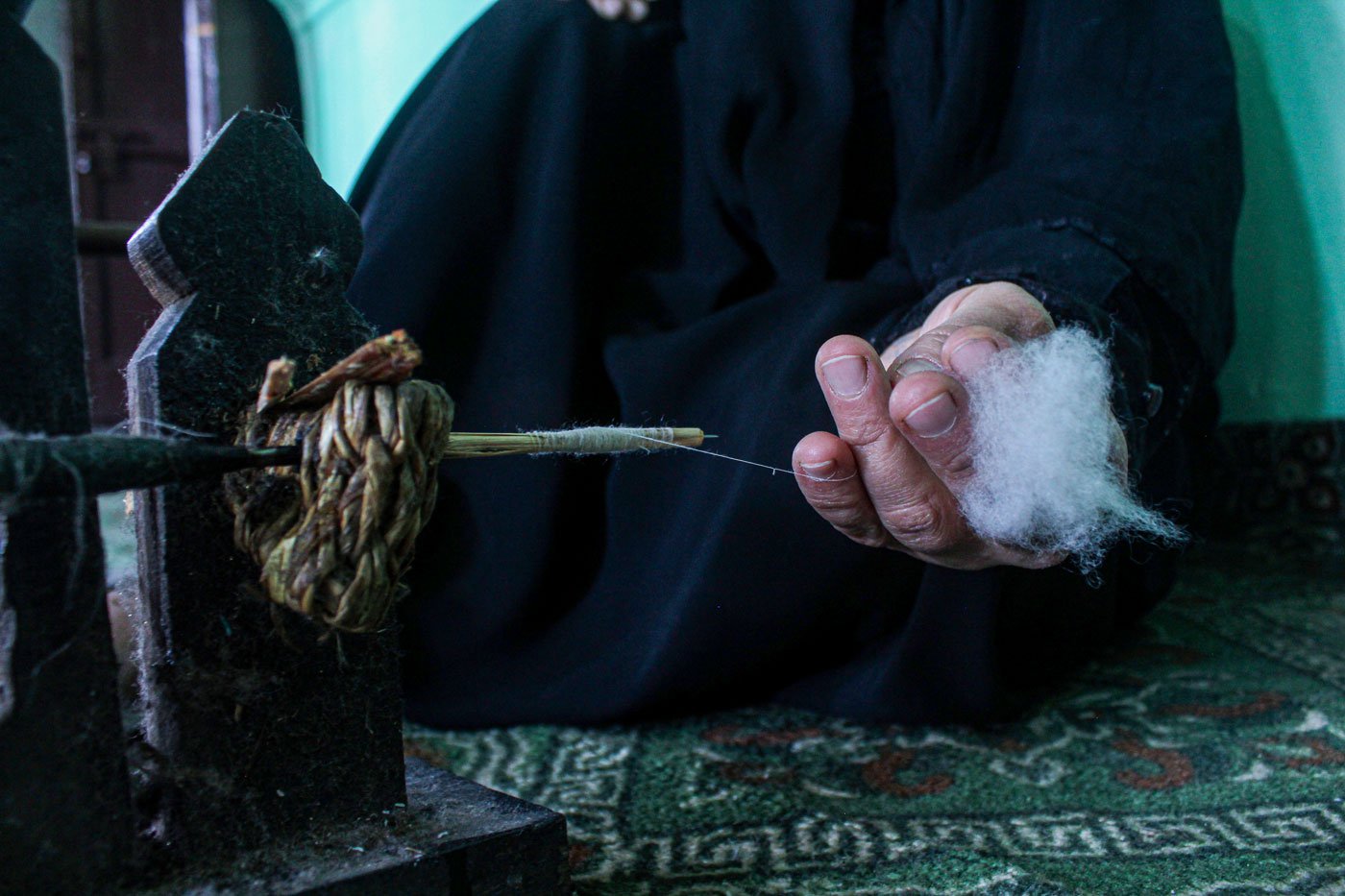
Left: Wool is pulled through a wooden comb to ensure the fibres are untangled and aligned. Right: It is then spun on a spindle made of dried grass stems
Making thread is a delicate and time-consuming job. “Two threads are combined to make one single thread for strength. Using a spindle, the two threads are twisted together and finally knotted,” points out Khalida Begum. She is a master spinner from the Safa Kadal area of Srinagar and has been spinning pashmina wool for 25 years.
“I can make 140-160 knots in one puri [10 grams of pashmina],” she says. Despite the time and skill required to do it, Khalida Begum earns only a rupee for one knot.
The price of pashmina yarn depends on the size of the thread – the thinner the thread the more valuable it is. A thinner thread allows more knots, a thicker one has fewer knots.
“In every knot, there are 9-11 threads of pashmina which are 8-11 inches long or equal to 8 fingers. This is how women measure the size of thread to make a knot,” says Intizar Ahmad Baba. The 55-year-old has been in the pashmina trade since his childhood. Each knot earns a hand spinner between Rs. 1 to 1.50, depending on the trader.
“A woman can only complete 10 grams of pashmina wool [into thread] as we have other household chores to do as well. It is nearly impossible to complete a puri a day,” says Ruksana Bano who is paid Rs. 1.50 per knot.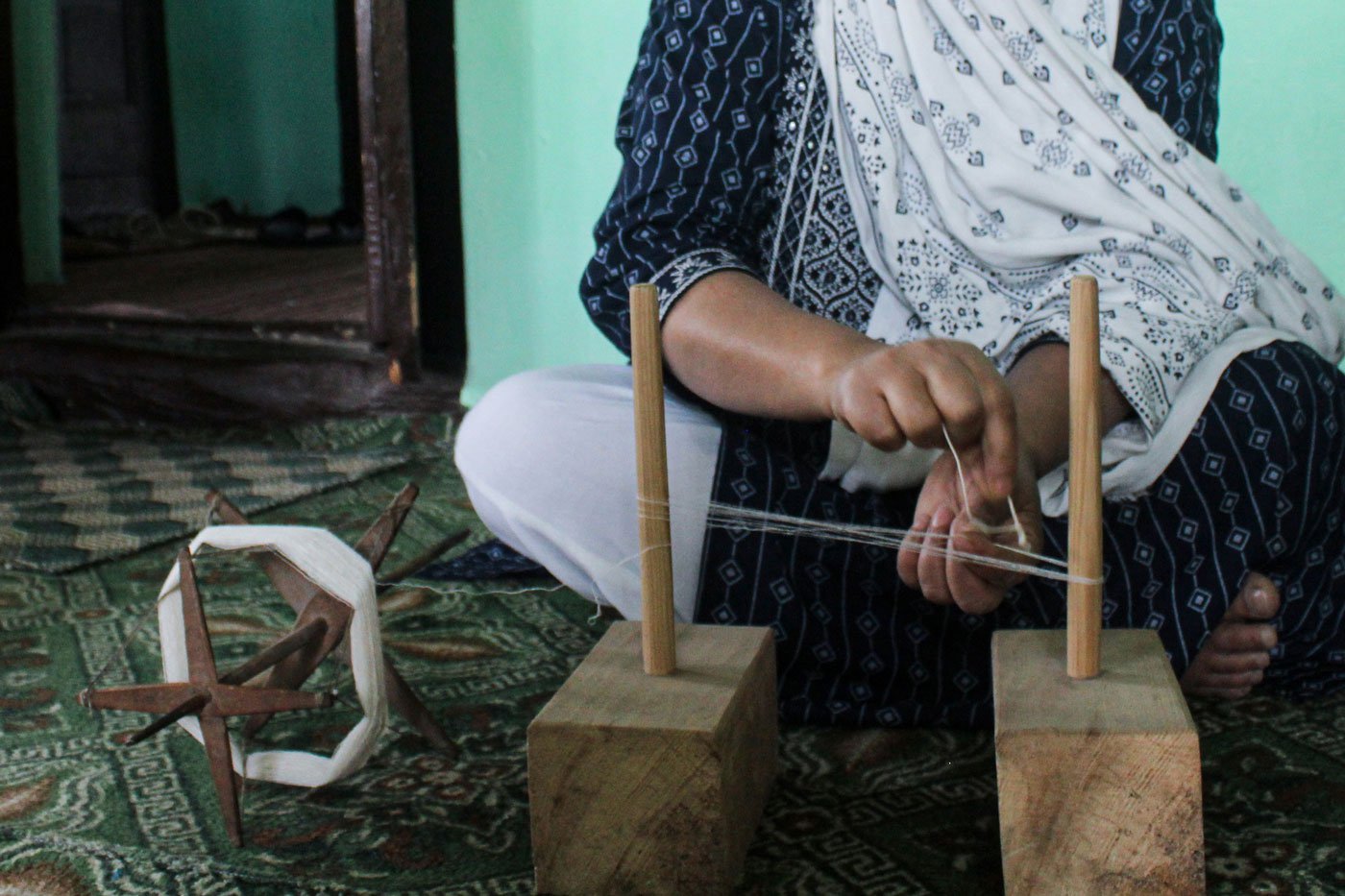
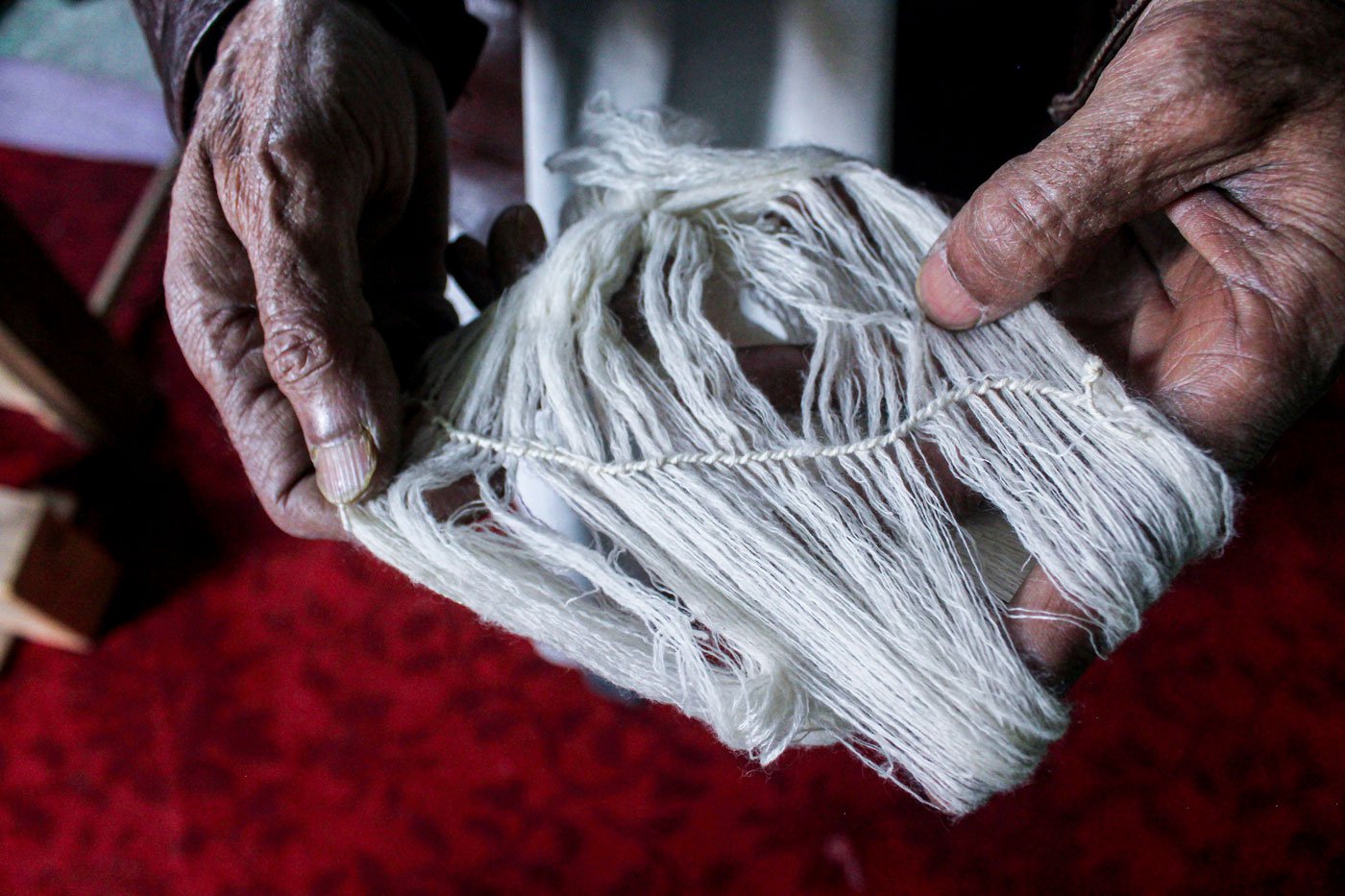
Left: 'I don’t think people will be doing hand-spinning of pashmina in the future,' says Ruksana. Right: Knots in a pashmina hand-spun thread
The 40-year-old Ruksana says at best she can earn 20 rupees a day from this work. She lives in the Arampora area of Nawa Kadal with her husband, daughter, and a widowed sister-in-law. “The most I have earned for weaving 10 grams of pashmina is 120 rupees for three days and I worked continuously from morning to evening with breaks only for tea and food,” she says. It takes her 5-6 days to complete 10 grams.
Khatija says pashmina weaving no longer fetches enough money: “Now I seem to work for days and earn nothing,” she says, recalling how, “Fifty years ago it was okay to earn 30 to 50 rupees a day.”*****
The poor wages for hand-spinning pashmina workers are because shawl buyers are not willing to pay the price. Pashmina trader, Noor-ul-Huda says, “When a customer gets the same machine-spun pashmina shawl for 5,000 rupees instead of a hand-spun one for 8,000-9,000 rupees, why will he pay more?”
“There are very few buyers of pashmina shawls that use hand-spun threads. I would say only two out of a 100 [customers] ask for an authentic hand-spun pashmina shawl,” says Noor-ul-Huda, 50, owner of a pashmina showroom, Chinar Handicrafts in Badamwari area of Srinagar.
Kashmir pashmina has a Geographical Indications (GI) tag since 2005. Final weaves using both hand-spun and machine-spun yarn are eligible for the GI tag, says a quality manual brought out by a registered body of artisans, and cited on the government website.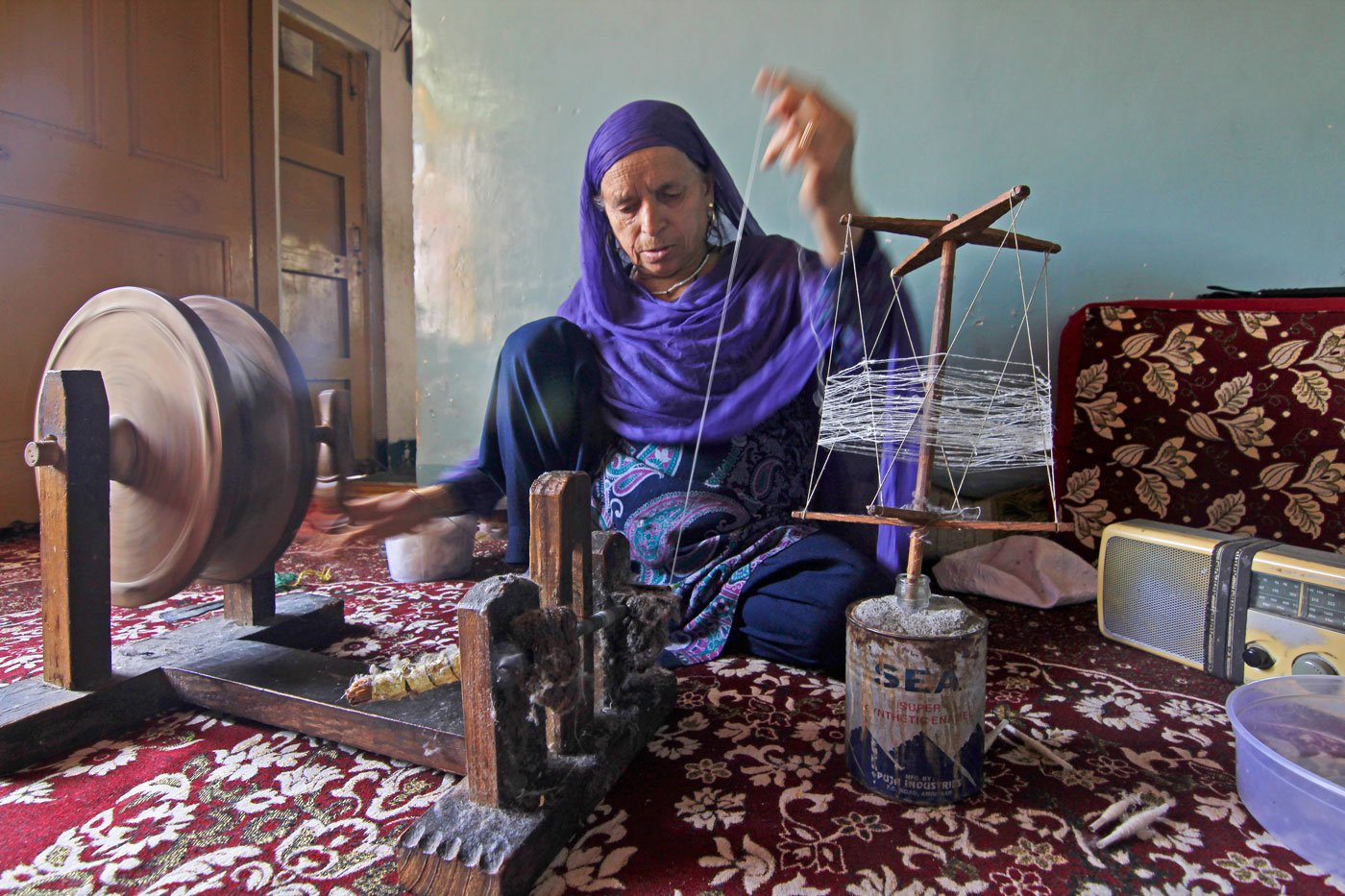
Combined threads must be twisted again on a spinning wheel so that they don't get separated
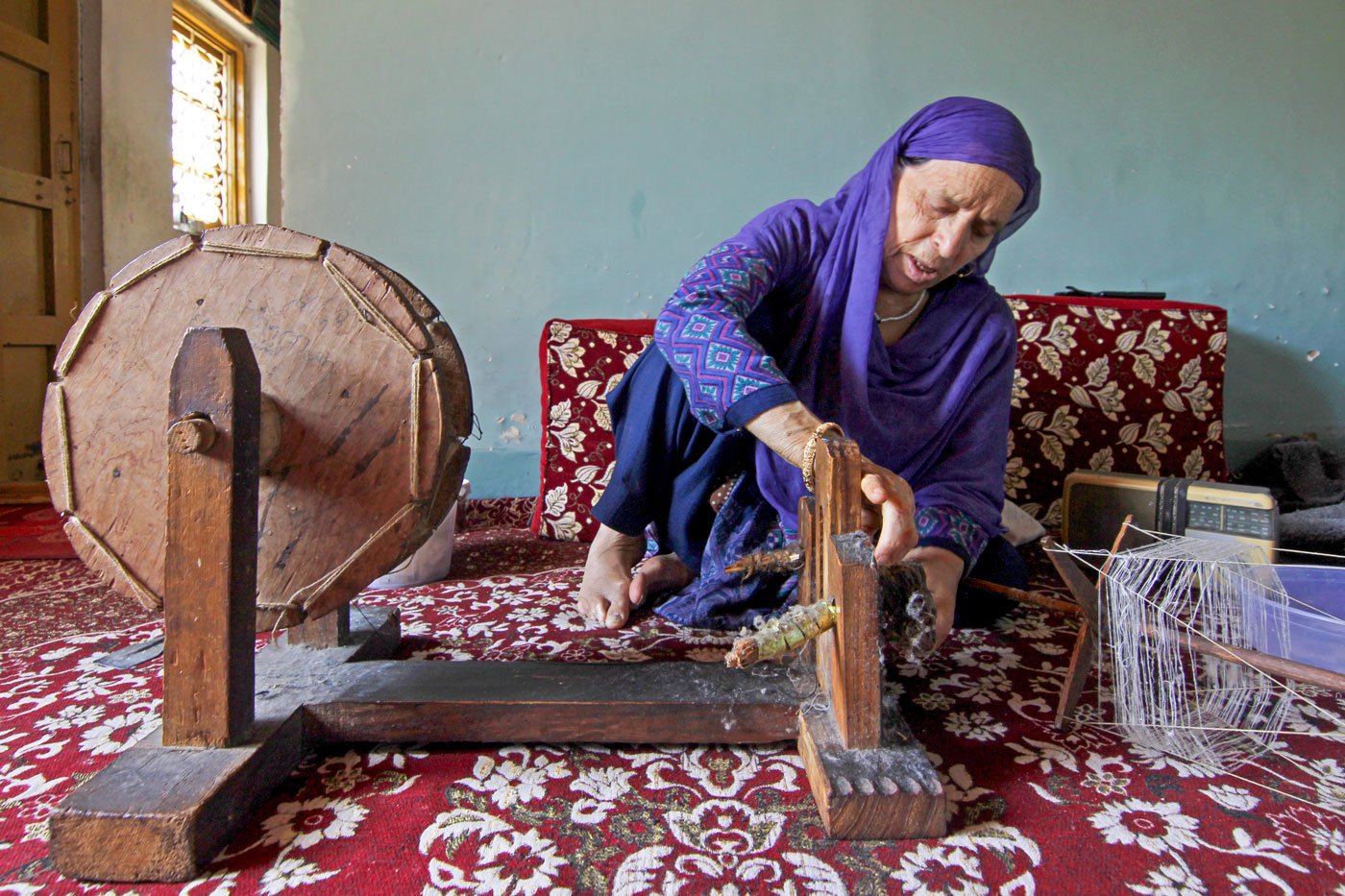
Khatija getting the spinning wheel ready to combine the threads
Abdul Manan Baba runs a century-old pashmina business in the city and has around 250 GI stamped goods – a very large number. The rubber stamp on the shawl guarantees that it is pure and handmade. But he points out that weavers prefer machine-made yarn. “The weavers are not ready to weave a pashmina shawl from hand-spun thread because of its delicate nature. Machine spun has an even thread and is easy for them to weave.”
Retailers often pass off machine-spun for hand-spun. “If we get an order of 1,000 pashmina shawls. How is it possible for us to fulfil it as it takes a minimum 3-5 days to spin 10 grams of pashmina?” Manan asks.
Manan’s father, 60-year-old Abdul Hamid Baba says that hand-spun pashmina is losing its appeal. He believes that the art of spinning was a gift from Hazrat Mir Syed Ali Hamdani, a Sufi saint who brought this art to Kashmir 600 years ago.
Hamid recalls how during his grandfather’s time people went to neighbouring Ladakh on horses to buy raw pashmina wool. “Everything was pure then, we had 400-500 women spinning pashmina wool for us but now there are only 40 women and they too do it because they have to earn.”